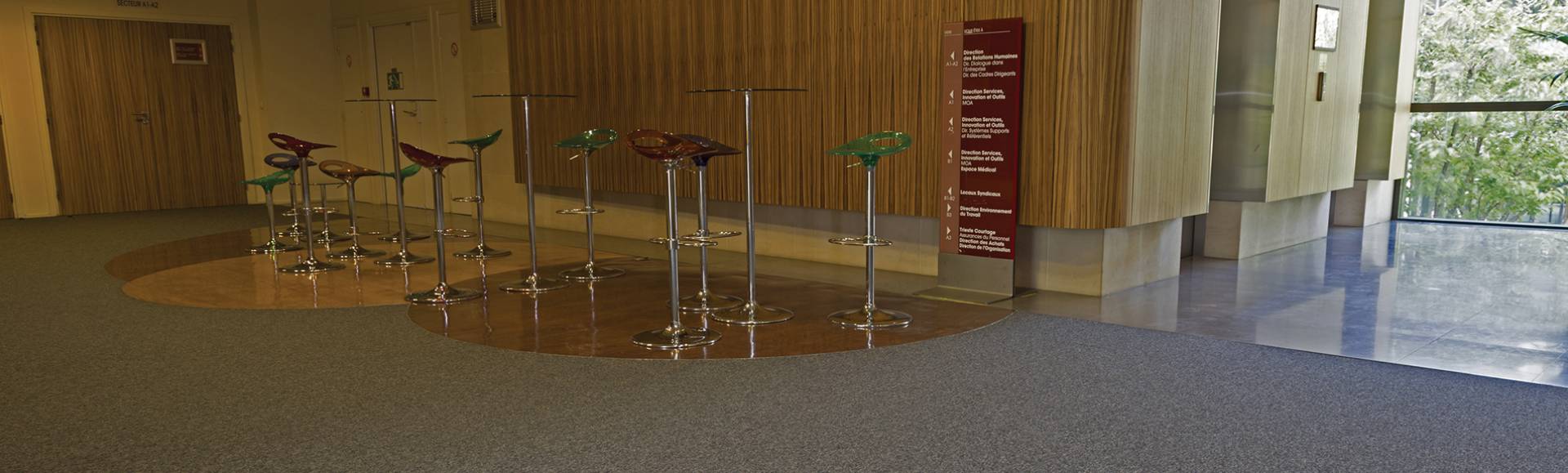
Generali - La Plaine Saint Denis
Place :
11-17 Avenue François Mitterrand 93200 St Denis - FRANCE.
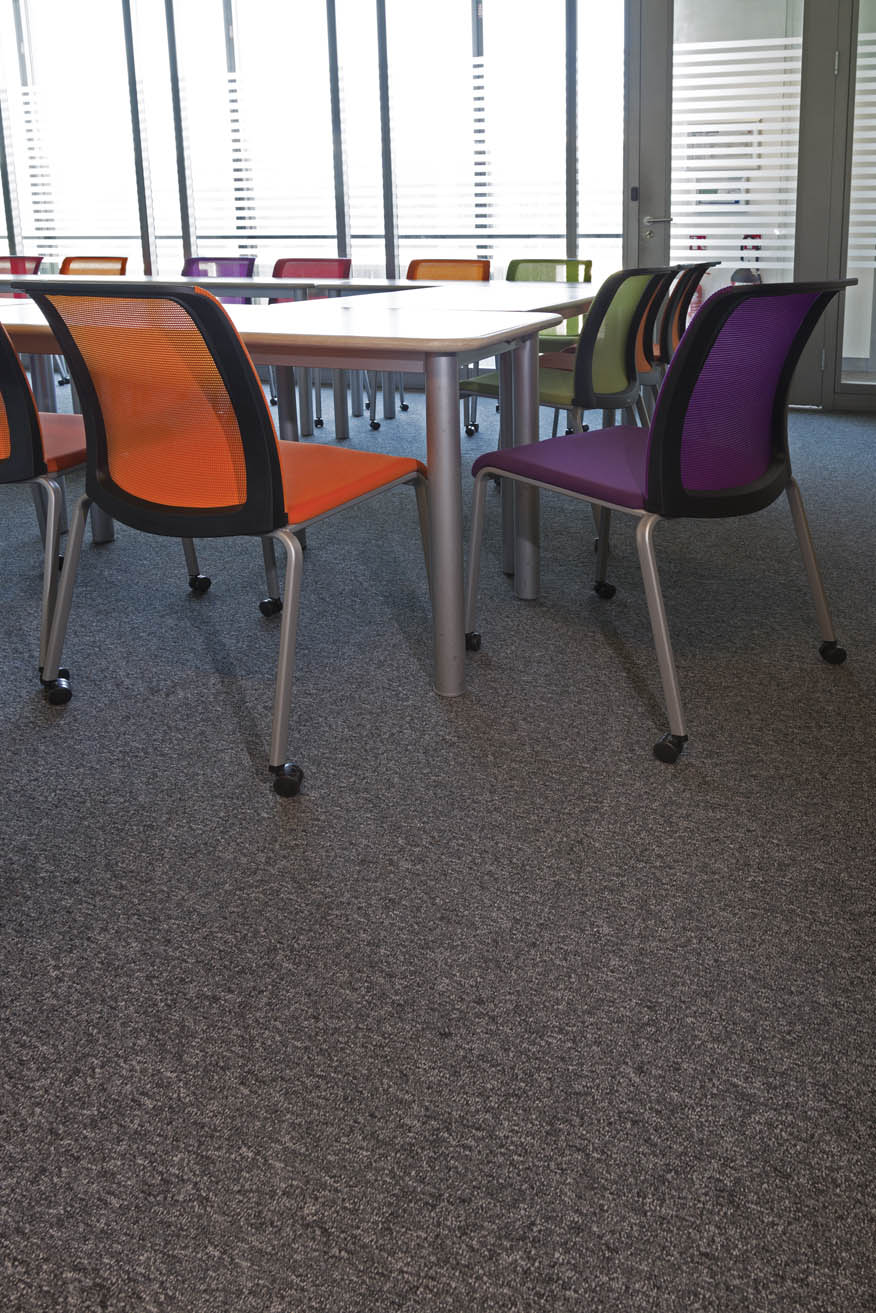
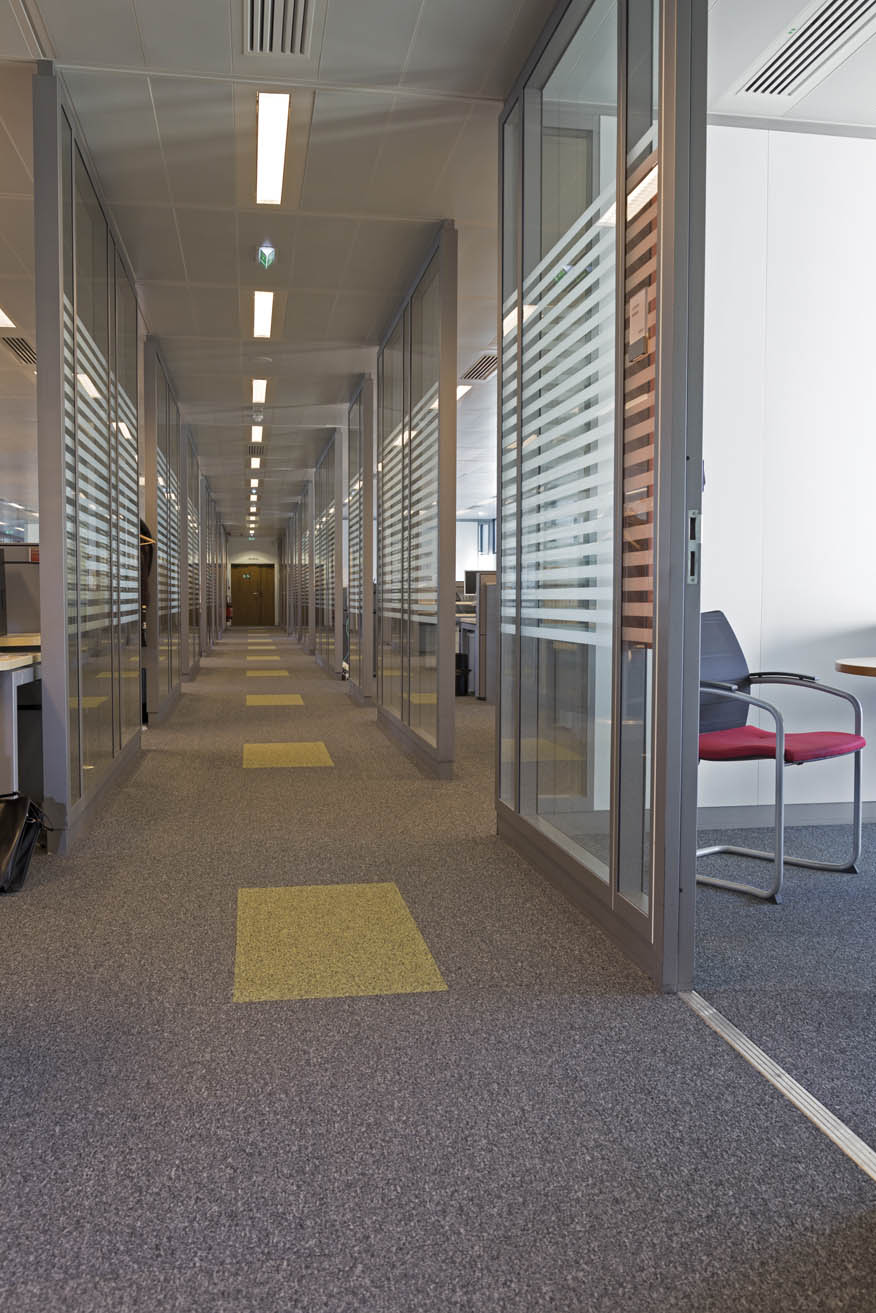
Interview – Generali Project :
- Mr Etienne LEGRAND (Work Environment Department - Head of Project Management)
- Mr Sylvain LEMAITRE (Work Environment Department).
1. What are your areas of responsibility and how is your department organised?
Etienne Legrand : We began work on renovating the flooring in 2012, and at the time, I managed the Relocation and Development department for Generali sites in the Ile de France region, meaning 6000 employees. 600 of these employees were located on Boulevard Haussmann while the remaining 5400 were at La Plaine Saint Denis (93) in a Campus comprised of 3 buildings (Innovatis, Jade and Wilo). In total, Generali boasts premises of 130,000 m² in France spread over a hundred sites.
Sylvain Lemaître : It is worth noting that the main carpeting renovation project mainly involves the Saint-Denis offices, as well as a few others located outside of the Paris area.
2. What was the driving force behind your search for materials?
Etienne Legrand : Generali opened its first office in Saint-Denis in 2003. Since then, no major renovation works have been carried out on the office floors. In 2012, the need for refurbishment was palpable. In 2010, we embarked on a quest to obtain HQE® [High Environmental Quality] Operations certification for the Saint-Denis blocks, with a view to improving standards in our employees' workplace, particularly in the open-plan areas.
We examined the different areas in which we could work to meet these two needs. The false ceilings over the floors required a single wash and were in perfect condition with the paint still very clean. That left the flooring to take care of, which comprised the biggest part of the project.
Although the insurance industry is not an excessively polluting area of activity, in the context of its Sustainable Development policy, Generali is committed to constantly seeking to reduce its environmental impact and has turned its attention to property. The HQE® Operations certification encourages us to take a responsible approach, and helped us establish a selection grid for materials and equipment.
3. What were your selection criteria?
Etienne Legrand : Starting off with a base material as a benchmark, we sought to improve properties and performance. For the textile tiles, we worked on several different aspects:
- Improving sound-proofing and acoustics,
- Using a product with reduced environmental impact (recycled content rate),
- Taking product recycling into consideration,
- Choosing a product that was easy to care for (choosing a more marled and darker shade than originally planned. A study on lighting revealed that 90% of surfaces were well-lit, so using a light colour wouldn't have been particularly useful),
- Showing consideration for people with reduced mobility (tests were carried out to check whether the carpeting could cause restrictive friction).
This analysis grid was a joint endeavour between the Purchasing department and Sylvain Lemaître and took into account all facts and figures. A RFI (Request for Information) was sent to manufacturers (Milliken, Desso, Balsan) and 3 products were selected.
4. How did Balsan meet your expectations?
Etienne Legrand : Balsan provided us with clear, pertinent answers with respect to recycling with Optimum, which allowed the carpeting to be recovered and reprocessed after use. The Re.Source range also met other criteria:
- a simple, understated range. The decorative, design element wasn't the most important factor in this case. We weren't looking for anything ostentatious or showy. We were looking to maximise our efficiency by enhancing maintenance processes in our offices, and in light of this, we opted for a single colour to reduce the amount of references to track and to avoid having to juggle special cases,
- undeniably improved acoustics and sound-proofing thanks to an integrated Sonic Confort sub-layer,
- EPD (Environmental Product Declaration) availability, which supplied us with all information concerning the product's environmental impact,
- the Re.Source range's GuT certification,
- the opportunity to forge a relationship with a French company that manufactures all of its products in France.
To maintain a level of cohesiveness, we also researched non-polluting floor primer products.
To reach a final decision, we worked alongside the Purchasing departments who pored over our suggestions and prices with suppliers. Once again, Balsan proved to be clear and precise with respect to their price offers.
5. How did the tile supply and implementation processes go in this site that was in use?
Sylvain Lemaître : Interventions in sites that are in use are always very complex to carry out. We could have gone for a methodical approach, moving from space to space, but this required establishing "buffer" and overspill zones, and meant moving people and furniture around twice, which would have resulted in significant additional costs.
After having looked at several possibilities, we decided to renovate the areas around staff turnover. Every year, an average of 3000 cases of staff turnover occur, and this is what dictates the pace of flooring replacement. Offices are renovated with the arrival of new occupants.
Almost all of the renovation work was carried out alongside turnover, with a very small proportion (1 to 2%) being carried out on specific areas irrespective of turnover.
Tiling and the removal of old tiles is managed by tiling companies (in the context of Optimum). These companies also take care of supplies by bringing the quantities needed for each intervention directly to the site. Balsan keeps a buffer stock of 1000m² in order to be able to meet requests quickly.
The two tiling companies we chose, Peinture Net and Prévotat, take care of storage and supply. Generali didn't want to be responsible for managing the stock.
It takes roughly one week to lay tiles in sections measuring between 500 and 800m². The carpeting is rolled out under the partitions when the partitions are shifted to the side.
A real implementation strategy was rolled out and communication with CHSCT was ensured.
To date (Editor's note: May 2014), 37% of the site has been renovated over the last 2 years (24,000 m²), with the target being 47% before the end of 2014.
85 tonnes of carpeting were removed and reprocessed. Optimum provided us with certificates to show the used tiles had undergone reprocessing.
By crossing the 50% flooring renovation threshold on the Wilo building, the latter's HQE® 'Integrated selection of building materials' has risen to High Performance level.
6. How was your business relationship with Balsan?
Etienne Legrand : Balsan injects a human element into its business relationships. Before work began, we felt the whole company was very actively involved. Stéphane Masson, representing Balsan's Technical Assistance and Geoffroy Bornard, Balsan's Production Factory Director came to visit our site with a view to understanding the context and to check whether the product would meet our requirements.
Follow-up is provided, which allows the company to respond quickly to any issues we may encounter over the course of a project on this scale. When a slight issue with gluing cropped up in a few areas, Mr Masson quickly responded with corrective action to be taken by our tiling teams.
Our sales contact was Ms Christine Nassour, who was always a pleasant, attentive and helpful contact point.
7. How satisfied are you and your employees ?
Etienne Legrand : Balsan's Re.Source textile tiles meet our needs, and more. Relocations are always an inconvenience for colleagues, and by demonstrating visible improvements to their working conditions (acoustics, comfort, cleanliness), we help them accept these changes more readily.
All of our employees are satisfied, and express how much better the acoustics and sound-proofing are now (footfall noise and airborne sound), which is very noticeable compared to our old carpeting.
And finally, by renovating our textile flooring, we've been able to boost our HQE® ‘Integrated choice of materials’ result up from Good Performance to High Performance, since over 50% of the surface area has been fitted out. HQE® certification boosts the value of the building in the event of a sale, and contributes to the value of our assets.
HQE® is both a label and framework within which we can progress in our operations: making continuous improvements to buildings. It allows the Property and Operations departments to measure our progress, and is considered as a management tool with which to establish employee priorities.
Done on 30/4/2014, CN and BS